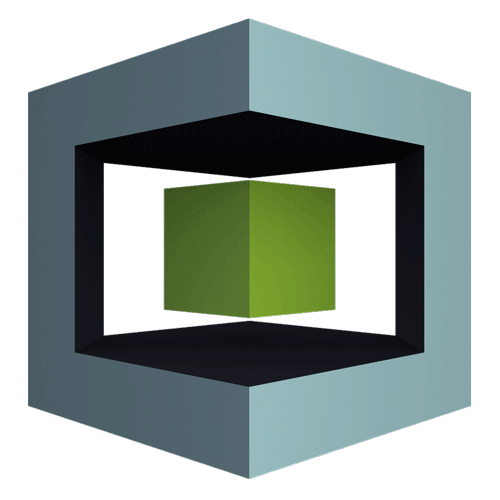
LOGISTICON AGRO
The control system of harvesting, sorting, storage and shipment of crops
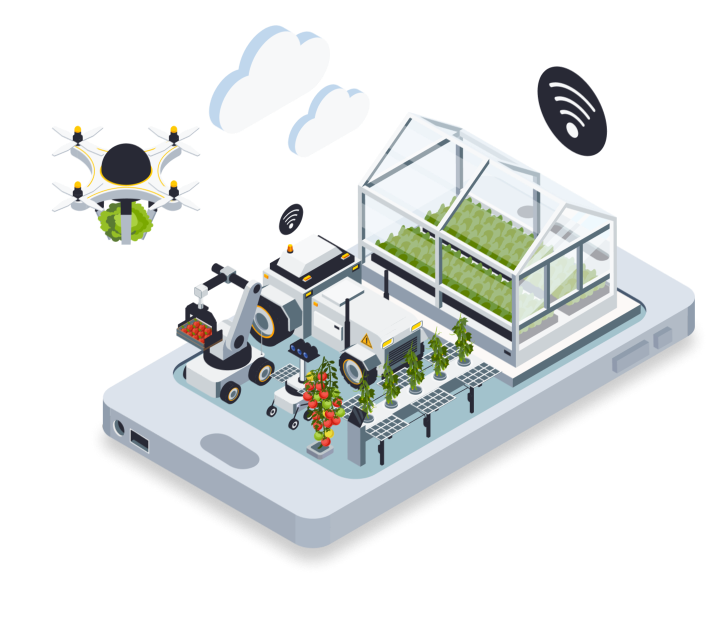
The LOGISTICON AGRO system is designed specifically for agricultural industry. Implementation of Logisticon AGRO allows you to solve the following tasks:

Accounting during harvesting (linking the varieties of grown products and the collected container to the planting map, weighing containers, moving them to warehouses).

Product identification. Products arrive at the warehouse taking into account additional information: quality status, batch number, expiration date and container weight.

Accounting for the sorting of collected products

Automatic preparation of relevant documents created on the basis of actually performed operations.
The principle of operation of LOGISTICON AGRO
- The system generates and prints unique labels with container numbers on special equipment. Before leaving for harvest, each container is marked with a corresponding label.
- After filling the container with the collected products, the shift foreman scans the bar code of the container and the bar code of the row with the help of a scanner. Data enters the system through the 3G mobile network. In this way, we know exactly what variety of product is in this container, the date and time of filling this container, as well as the name of the foreman whose people harvested this crop.
- Containers are moved to the weight control zone, which is connected via WiFi to the servers of the cloud system. The storekeeper scans the unique number of the container and presses the "get weight" button (data is not entered manually). Data on the time of weighing and the name of the storekeeper are similarly stored in the database.
- The storage location - the field - is automatically obtained. After moving to the selected warehouse, the number of the container and the bar code of the warehouse area where it was placed are scanned. Therefore, the system stores information about who moved the container and to which warehouse.
- Containers are selected for product sorting, their unique number and barcode of the sorting line are scanned. In this way, the container is moved to the sorting warehouse. After sorting, the received pallets with finished products are marked with new unique numbers, this number and the bar code of the composition of the finished products are scanned.
- Received pallets are moved to the warehouse for shipment to end customers.
- On the basis of the received data, it is possible to conduct an analysis of the yield for each specific planting row, and agronomists will be able to quickly make appropriate decisions. For each harvesting team, there will be an automatic fixation of production by weight, which will allow to evaluate efficiency and more accurately calculate wages. Weight control will strengthen.
The system implementation will allow tracking the entire chain “from the tree to the store counter"